This article introduces a more detailed description of Sapotech’s Reveal TAP for Ladle Well Area Monitoring, explaining its functions and different benefits that it brings to its users. From improved ladle opening rates to real-time feedback and systematic documentation, this system’s potential in the field of steelmaking will be presented.
Description
Maintaining a high free opening rate of ladles is a key factor in the steelmaking process for both ensuring steel quality and safety. Steelmakers rely on well fillers to prevent direct contact between the molten metal and the ladle’s slide gate-system. However, it’s not only about the quantity of well filler, the quality and correct positioning are equally crucial to protect the slide gate effectively. Before adding the well filler, it is essential to check that the well block is clear from any remaining steel or slag. Sapotech’s Reveal TAP for Ladle Well Area Monitoring can be used for this purpose. This automatic monitoring system can be utilized to systematize the process of well filler addition, and to analyze the ladle bottom, particularly the well block area, both before and after the addition of filler sand.
The system recognizes when the ladle arrives at the sand addition location and automatically starts the imaging. From the live view, the user can verify the correct position of the ladle before adding sand and adjust the position if necessary. Following the sand filling, the user can view images of the bottom of the ladle in the user interface, both before and after the sand filling process (Figure 1).
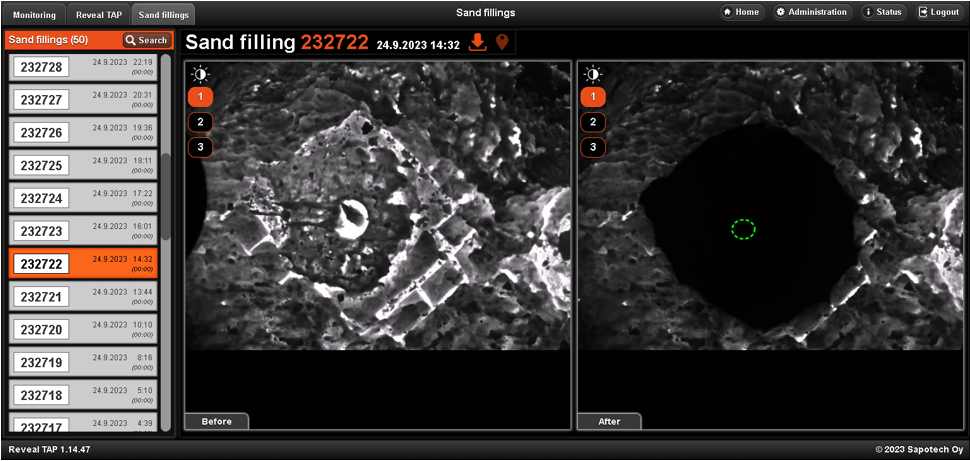
Figure 1. Well block area before and after sand addition visualized in Reveal TAP user interface.
Next, the functions of the system are presented in more detail, along with the benefits that can be derived from its implementation.
Application
Among Sapotech’s systems, ladle well area monitoring system is one of the easiest to install and take into use. Only power and compressed air are required from the customer. The high-resolution industrial camera is positioned perpendicularly to the bottom of the ladle to monitor the well block area. An edge computing unit processes the images, analyzes the condition of the well block area before and after sanding, and provides the user interface to review the sanding hit rate. All the configuration work can be done via Sapotech provided VPN device, so there is no need for IT department to configure secure connections. The system can therefore be isolated from the company network, providing a stand-alone solution for the ladle preparation area. Figure 2 shows an example on how the well-filler camera can be located. Figure below shows an installation where semiautomatic feeder is used to fill the well block area, however, Sapotech monitoring system can also be used in case of manual sanding where operators throw the well filler bags to cover the block area.
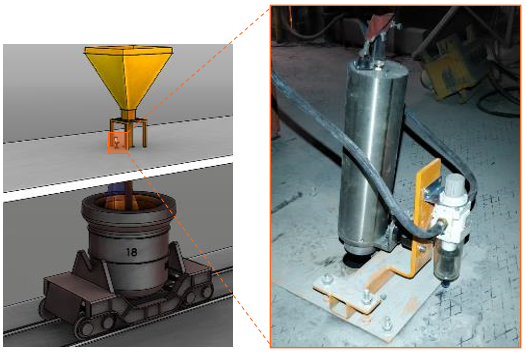
Figure 2. Camera positioning to monitor the well block area and sand addition.
The Reveal TAP system for ladle well area monitoring provides the following information:
- Visualization of the process: High precision and real-time visualization of the ladle bottom area (well block) condition.
- Ladle positioning assistance: Providing live view to assist in the positioning of ladles for well filler sand addition.
- Automatic imaging: Capturing images automatically of the well block area both before and after the addition of filler sand.
- Cleanliness analysis: Well block is analyzed to see if there is any remaining steel or slag.
- “Hit rate” analysis: Assessing the “hit rate” to ensure accuracy and effectiveness in the well filler sand addition process.
- User-friendly interface: Allowing access and sharing of information through the Reveal Platform.
- Traceability: Enabling traceability back to individual well filler sand additions through a search function in the Reveal user interface.
In the next chapter, we will discuss more about the benefits obtained from the system.
Benefits
Sapotech’s Reveal TAP for ladle well area monitoring offers the following benefits to its users:
- Increased ladle free opening rate: Achieved through more precise well filler addition, ensuring the quality of steel.
- Live view for lade positioning: Facilitates easier ladle positioning for well filler addition.
- Real-time feedback on slide gate area: Gives operators immediate feedback on the condition of the slide gate area.
- Systematic documentation: Enables systematic documentation for process tracking and optimization.
- Recordings: Every well filler sanding recorded and accessible.
- Savings in process breaks and damages: Results in decreased process breaks and minimizes damages to refractories and ladle shell, leasing to cost savings.
- Improved worker safety: Enhances worker safety near the steelmaking processes.
- Easy information sharing: Sharing of information via Reveal Platform.
- Fast and easy implementation: Quick and straightforward installation of the system.
- Multi-camera approach for porous plug monitoring: Offers the option to implement a multi-camera approach for monitoring the condition of the porous plug as well.
In conclusion, Sapotech’s Reveal TAP for ladle well area monitoring is a simple yet powerful system, offering users a well-designed tool to elevate their steelmaking processes.
If you have any questions about the article or the Reveal TAP system, don’t hesitate to contact us.
Stay tuned for our latest articles and news by following our LinkedIn page!